Research impact: Enabling companies to use flow modelling in product design
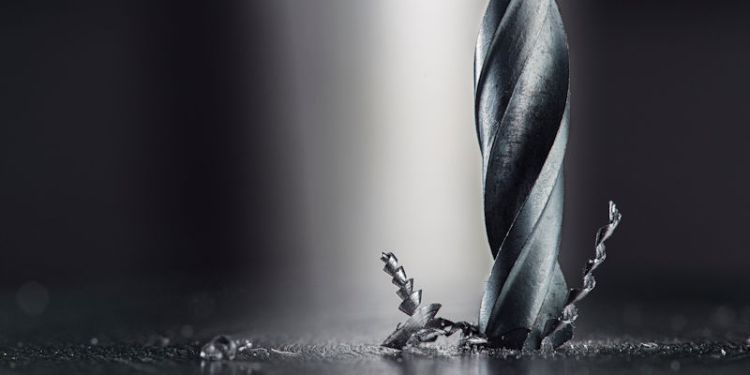
Computer based flow modelling research, developed at the Schools of Mechanical and Civil Engineering, is enabling companies in the commercial and public sectors to improve their products. This has resulted in improved products for a range of companies in the commercial and public sectors.
Based on theoretical methods of how fluids and gases will flow through a range of systems, the University team has created new ways for companies to access flow modelling data and build it into their design processes.
Professor Harvey Thompson, from the School of Mechanical Engineering, says: “Generally, industry doesn’t want to wait for days or weeks to do practical flow simulations – but they need the data from the simulations so that they can design their parts. Our work helps them access that quickly and easily.”
Industry... need the data from the simulations so that they can design their parts. Our work helps them access that quickly and easily.
In a recent collaboration with Swedish machine tool company Sandvik Coromant, Professor Thompson and colleague Dr Jon Summers helped to solve an issue with its high-performance machine twist drills. These precision drills are used in the final stages of manufacturing of high value components, such as composite airplane wings. The high temperatures generated by drilling mean the drill part must be cooled with oil so that it does not break. Previously, huge quantities of oil were used to flood the drill as it works, which is messy and inefficient.
Professor Thompson explains: “We wanted to come up with a design where the liquid cools the right areas, so we used computer modelling that indicated the best place for the liquid to go, using the data from lots of simulations.
We wanted to come up with a design where the liquid cools the right areas, so we used computer modelling that indicated the best place for the liquid to go, using the data from lots of simulations.
When tests confirmed that the simulation models were reliable, the company went on to use the technology to design better functioning drill bits, with holes through which liquid can be precisely directed. This has resulted in a step change in reliability and durability of the drills, helping the company to predict with confidence how they will perform in manufacturing processes. Subsequently, Sandvik Coromant decided it needed to set up its own flow modelling simulation group in Sweden and the Leeds researchers helped to train the simulation group professionals.
Another company benefitting from Leeds expertise is Parker Hannifin, a manufacturer of filtration systems for diesel engines which enable reductions in emissions to meet European standards. In order to ensure competitiveness, the company wanted to make sure that its energy efficiency was as high as possible. Working with the company, Professor Thompson and Professor Nik Kapur used their expertise on gas-liquid flow to develop an accurate computer-based flow modelling methodology that could be used to find out how the shape and geometry of the jet pump in the filtration system affected pressure changes and shock wave formation inside it.
Professor Thompson says: “Again, it was the use of the computer programme which meant they could design it for themselves. They didn’t need to do all the high level flow modelling; they could simply exploit it to come up with a family of products that were more competitive.”
The flow-modelling programmes have also been used outside the engineering industry, such as assisting the Yorkshire Ambulance Service to reduce the aerodynamic drag of its light bars on the roofs of its vehicles.

The flow-modelling programmes have also been used outside the engineering industry, such as assisting the Yorkshire Ambulance Service
Work completed through a Knowledge Transfer Partnership set out to improve the aerodynamic design of ambulances, which was subsequently validated by wind tunnel experiments. Simple changes led to over 12% improvement in the ambulance’s fuel economy, saving the service approximately £300,000 a year. As a result, the local ambulance service commissioned more aerodynamically efficient ambulances.
Professor Thompson concludes: “Often the impact of this work is that it can provide evidence and therefore an incentive to make better decisions, or change specifications, if none existed before.”
Contact us
If you would like to discuss this area of research in more detail, please contact Professor Harvey Thompson.