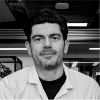
Professor Robert Kay
- Position: Professor in Advanced Manufacturing
- Areas of expertise: Digital Fabrication; Additive Manufacturing; 3D Printing; Manufacturing Processes Research; Advanced Ceramics; Electronic Systems.
- Email: R.W.Kay@leeds.ac.uk
- Phone: +44(0)113 343 2139
- Location: G.34 SCaPE
- Website: Future Manufacturing Processes Research Group | Videos | LinkedIn | Googlescholar | ORCID
Profile
I am a Professor in Advanced Manufacturing at the University of Leeds with extensive experience in manufacturing processes research both in industrial and academic environments. Throughout my career, I have developed disruptive manufacturing techniques and exploited these ideas to benefit industry, society and scientific research. During my doctoral studies, I developed a novel electroforming process: (R. W. Kay, “Electroformed component manufacture.” WO Patent WO2007063331A1, 12-Aug-2004). To commercialise my research, I founded MicroStencil Limited in 2003, where I secured equity funding [Herald Scotland News Article], scaled the technology for commercial production, built a diverse customer base with leading electronic manufacturing firms, and established a manufacturing partnership licence in Asia. This commercialisation experience which spanned the development of a new manufacturing concept through the full Technology Readiness Levels (TRL1-9) formed the basis of an industrial case study for Heriot-Watt University under REF2014.
With a combined background in fundamental scientific research and enterprise, I started my first academic post in 2012 with the vision of interleaving disparate digital fabrication processes to create new capabilities within engineered functional devices. This vision allowed me to secure blue-sky funding routes within the Engineering and Physical Sciences Research Council (EPSRC) as Principle Investigator to successfully develop speculative manufacturing concepts, and to work with a range of industrial partners, translating academic research into the engineering sector. In particular, this funding aided the development of fundamental science in additive manufacturing and direct write processing. This synergistic combination has enabled multi-material arrangements and compositional complexity which aims to provide transformative routes for producing next-generation products.
I have published over 85 journal and conference papers covering topics in manufacturing, materials, electronics, computational modelling, and chemistry. I am a very active participant in my research community with success in all my projects driven by multi-disciplinary, collaborative teams that include academic institutions, industrial partners, High-Value Manufacturing Catapults, and NHS clinicians. I am also keen to inspire the next generation into science and engineering through research-led teaching, research lab placements and outreach activities. I represent the University of Leeds on the British Standards Institute Committee AMT/8 Additive Manufacturing and the International Organization for Standardization ISO/TC 261/WG 2 panels helping to develop standards for the community.
Responsibilities
- Director of the Institute of Design, Robotics and Manufacturing
- School Deputy Director for Research and Innovation
- Promotion Panel Grade 8 and 9
Research interests
My research is focused around developing digital fabrication processes for the manufacture of functional devices spanning a range of application areas and industries including high-performance ceramics, medical devices, electronic systems and wearable technology.
Current Research includes:
- 3D Manufacture of Advanced Engineered Ceramics
- Digital Fabrication of high-performance electronics
- Robotics in manufacturing
- Creation of condition monitoring systems for orthopaedic implants
- Hybrid Additive Manufacturing Processes Research
I am the Technical Lead for the University of Leeds on the £22.6m Strength in Places Fund Advanced Manufacturing Productivity Institute.
<h4>Research projects</h4> <p>Some research projects I'm currently working on, or have worked on, will be listed below. Our list of all <a href="https://eps.leeds.ac.uk/dir/research-projects">research projects</a> allows you to view and search the full list of projects in the faculty.</p>Qualifications
- PhD in Electroformed Stencil Manufacture using Microfabrication techniques
- Beng Electrical and Electronic Engineering
Student education
Theme lead - Additive Manufacturing
The School of Mechanical Engineering has 40 x 3D printers used solely to support practical teaching. The School also runs a 3D Printing bureau services available to over 1000 students. This service allows students and academics to make printing requests and typically receive their prints with 1-2 working days. These facilities have transformed the way students can conduct projects at the University allowing them to rapidly secure tooling, fixtures, jigs and experimental samples while also reducing the burden on the mechanical workshop.
Module leader for MECH3775 – Additive Manufacturing
20 credit module, 3rd year Undergraduate. Covering degree programs: Mechanical Engineering, Medical Engineering, Product Design Engineering, Mechatronics and Automotive.
Class size: 2020/21 – 310 students, 2021/22 – 260 students, 2021/23 – 275 Students
To prepare the next generation of graduates with the skills for working in industry I deliver a module solely focused on Additive Manufacturing, 3D scanning and other advanced manufacturing approaches. The module content incorporates research led lecturing and inclusion of the latest developments in industry, interactive learning and hands on practical sessions that directly support the taught curriculum. Students also benefit from invited relevant industrial speakers as experts in the field to talk and debate with the class and linked in the latest standards from the field stemming from my role on the British Standards Institute Additive Manufacturing Committee. The module embraces digital technology to enhance the learning process with a detailed VLE enhanced with infographics and videos.