Automotive Braking
Multidisciplinary optimisation
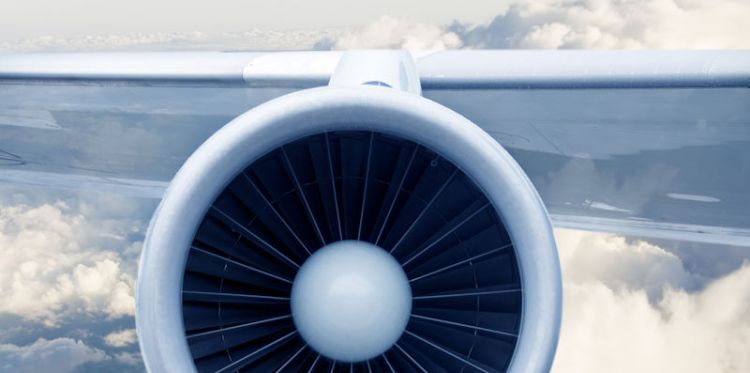
Optimisation is a methodology, which allows any performance measure of a process or a product to be maximised or minimised, allowing any resources required to be efficiently used with minimal impact on the environment.
Multidisciplinary optimisation is a methodology which uses the interdisciplinary interactions of the applications of a structure, component, system, process or design in order to improve its overall performance.
If performance evaluation of the object/process requires significant computing time, it is necessary to develop and use metamodels. They allow the complex behaviour of the system to be represented with simpler, computationally inexpensive and relatively noise free models obtained, for example, by Genetic Programming, Moving Least Squares Method or based on the interaction of low- and high-fidelity simulation models. Different optimisation techniques including evolutionary algorithms and gradient-based methods can then be used to find the optimum on these metamodels. Such models are also applicable for stochastic analysis and optimisation, where for example a large Monte Carlo simulation can be performed to assess reliability and robustness of a system or a process.
Multidisciplinary optimisation research spans several areas. Development of the metamodel-based infrastructure for multidisciplinary applications is one of the major activities in the group.
Another major activity is the development of a large-scale optimisation technique (100s of design variables) based on the mid-range approximation method (MAM). To deal with the curse of dimensionality, approximations in MAM are based on intrinsically linear functions as well as simple rational functions and moving least squares approximations with a linear base function. The final approximation is arrived at using an adaptive selection and regression-based model assembly. This approach was successfully used on a number of live design projects at Rolls-Royce where a single simulation took tens of hours, with a performance orders of magnitude faster compared to other optimisation techniques. This technique can handle other major issues arising in industrial applications such as numerical noise and occasional simulation failures.
This expertise is complemented by experience in topology optimisation, which has been applied to a number of areas such as the aerospace and civil engineering industry. We also engage in collaborations with industry providing specific expertise in multidisciplinary, structural and fluid dynamic optimisation.
Research projects
- TSB and Rolls-Royce, SILOET-2, Development of stochastic optimisation methodology for turbomachinery applications, £256,000 (2013-2016).
- Marie Curie ITN AMEDEO Aerospace Multidisciplinarily-Enabling Design Optimisation, Coordinator. 3.6M, partners DLR, ONERA, Rolls-Royce, Altair, ALE, Von Karman Institute, TU Delft, TU Munich, Airbus France (2012-2016).
- ALaSCA Advanced lattice structures for composite airframes, EU Programme Transport (including Aeronautics), Partner 194,400 (2010-2013).
- KTP project KTP008074 with EADS Innovation Works (UK) Development of automated structural optimisation process for small aerospace parts, £138,123 (2011-2013).7
- Knowledge Transfer Secondment (KTS) grant Aerodynamic drag reduction of emergency response vehicles through multidisciplinary design optimisation, Yorkshire Ambulance Service, £55,959 (2010-2011).
- DTI CFMS (Centre for Fluid Mechanics Simulation) Core Programme TP/L3001H. Co-sponsored by Rolls-Royce plc and Airbus UK Ltd. Development of large-scale optimisation techniques for aerothermal design systems. £250,000 (2007-2010).
For more information contact Professor Ozvaldo Querin.